1. Transfer printing. First, the pigment is printed on the paper by printing method to make transfer printing paper, and then the color is transferred to the fabric by high temperature (heating and pressurizing on the back of paper), which is usually used in chemical fiber fabrics, characterized by bright colors, fine layers and realistic patterns. Art is strong, but the process is only suitable for a few synthetic fibers, such as polyester. Transfer printing process is simple, and has characteristics of small investment, flexible production, which is currently more popular in the market. To be honest, however, the price is a little higher than the other types of printing, but there are certain grades.
2. Planting beads. Bead planting is a high-demand process, now only a small number of factories can do well, the general factory is almost no such this process. Bead planting is also called toothbrush flower, and the finished product is named as a toothbrush whisker with a root standing up. I heard that a flower has to be printed 20 or 30 times before it can be printed well. The height of the finished product can reach about 0.3CM, and the top of the product is bead-shaped. You can do other colors on top, as if carrying beads, so it is also called planting beads.
3. Bubble pulp. Bubble pulp, as its name implies, is even the foam pulp, which is also changed by the glue. First, the mixed pulp is printed on the clothing material, and then processed by the high temperature machine, and the pattern is bubbled up. The stereoscopic feeling is very good, and it is a little soft. But after the clothes are washed many times, the three-dimensional effect will slowly disappear and flatten.
4. Pigment printing. Because pigment is a non-water soluble colouring material and has no affinity to fibers, and its coloring depends on the coating of film-forming polymer (adhesive) and adhesion to the fiber. Pigment printing can be used in the processing of any fiber textile, and it has more advantages in the printing of blended and mixed fabrics, and the process is simple, the chromatogram is wide, the flower outline is clear, but the handle is not good, and the rubbing fastness is not high.
5. Shrink printing. The use of locally applied chemicals on the fabric by printing to cause the fiber to expand or contract by proper treatment, to cause the difference in the expansion or shrinkage of the fiber in the printed part and in the fiber in the non-printed part. Thus, the products with regular concave and convex patterns on the surface are obtained. For example, pure cotton printing foam yarn with caustic soda as expanding agent.
The article comes from the internet
.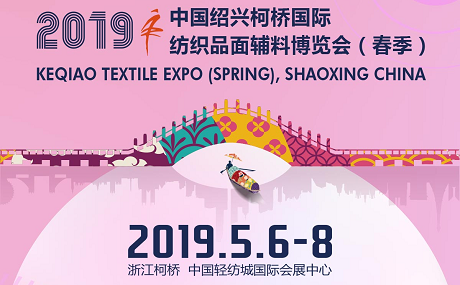